You will find the work of a wiring harness manufacturer underneath the sleek exterior of every vehicle, where a sophisticated network of wires is meticulously orchestrated to bring life to the machine. These intricate systems, known as wiring harnesses, are the unsung heroes that power the heartbeat of automotive manufacturing. Today, we delve into the realm of these technological marvels, uncovering the enigmatic world of the masterminds behind them – the wiring manufacturers.
Imagine a symphony of precision engineering where every conductor plays a vital role in harmonizing the complex operations of a car. This post highlights the automotive industry’s artisans who craft these lifelines of electricity and data.
Join us on a journey through the meticulous craftsmanship, innovative technologies, and untold stories that shape the backbone of modern vehicles, all woven together by the expertise of the elusive wiring manufacturer. Let’s unravel the mysteries behind the scenes and spotlight the ingenuity that propels the automotive world forward.
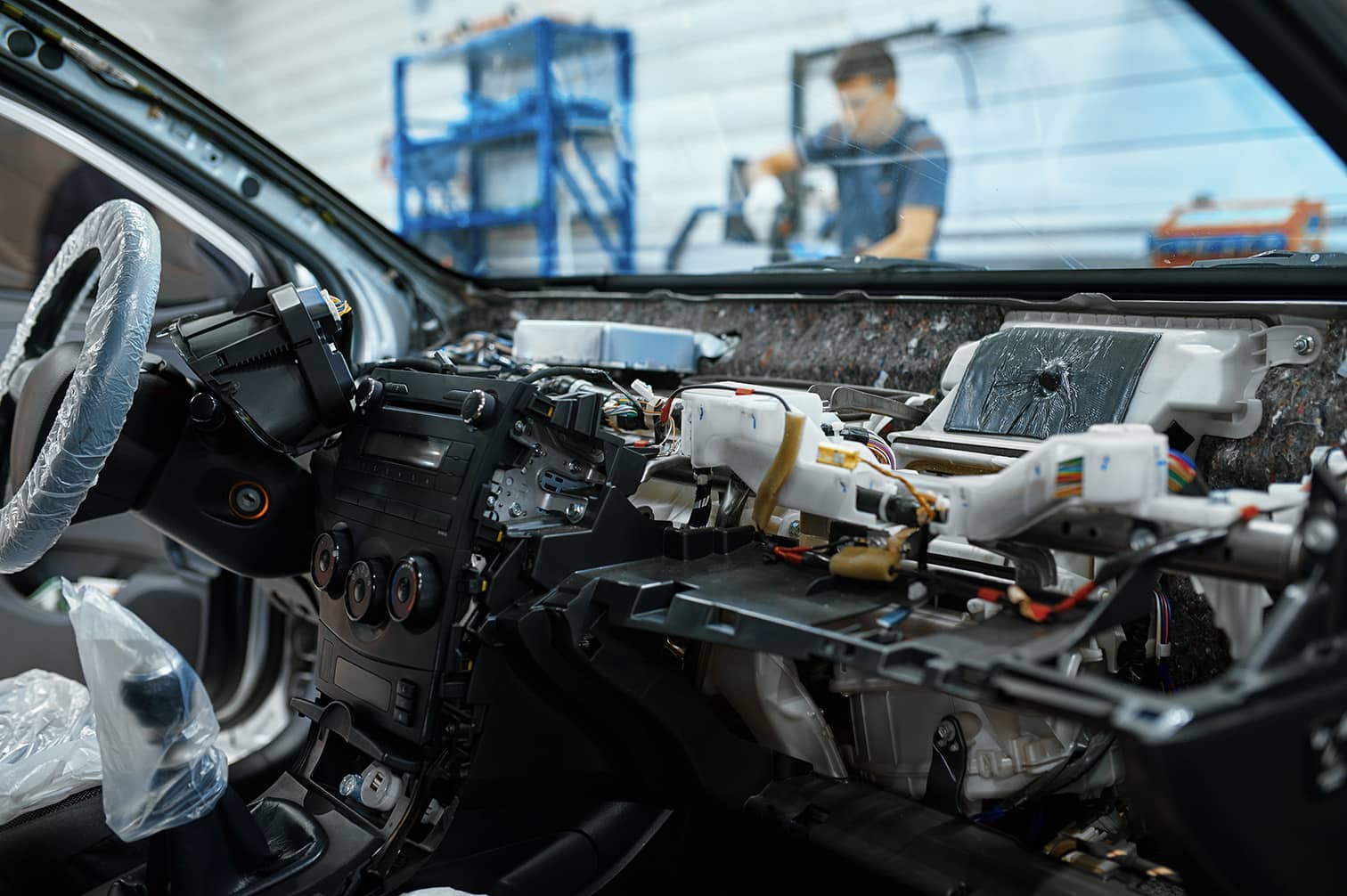
The Evolution of Wiring Harnesses in Automotive Manufacturing
Wiring harnesses have come a long way since their inception in the early days of automotive manufacturing. Initially, these harnesses were simple and rudimentary, consisting of basic wires bundled together to connect various electrical components of a vehicle. However, the need for more sophisticated wiring systems arose as technology advanced and cars became more complex.
With the advent of computer-controlled systems and advanced electronics in cars, harness manufacturers had to adapt and innovate. They began incorporating specialized connectors, sensors, and modules into their designs to accommodate the growing complexity of modern vehicles. This evolution allowed for better integration between different components and improved overall performance.
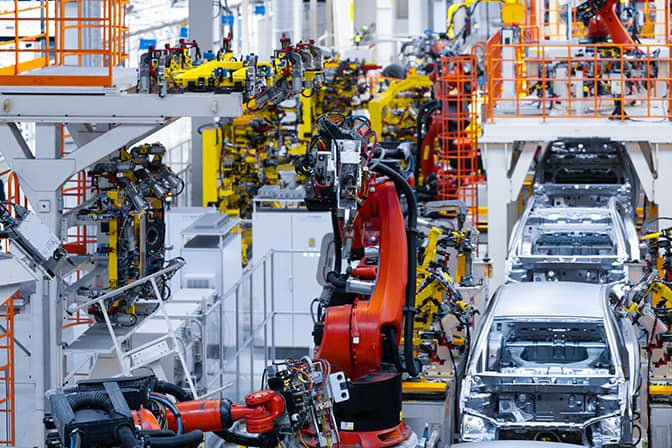
Furthermore, advancements in materials and manufacturing techniques played a crucial role in the evolution of harnesses. Manufacturers started using high-quality wires with superior insulation properties to ensure durability and longevity. They also implemented automated production processes that enabled faster production times while maintaining strict quality control standards.
Today, wire harnesses have become highly intricate systems that transmit electrical signals and facilitate data communication between various vehicle components. These harnesses are meticulously engineered to withstand harsh environmental conditions such as extreme temperatures, vibrations, and electromagnetic interference.
Behind the Scenes: Crafting the Lifelines of Modern Vehicles
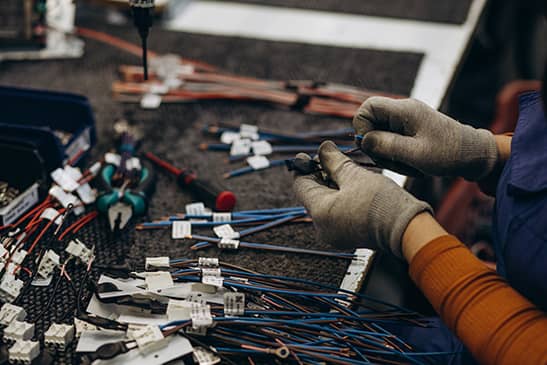
The process of crafting a wiring harness is meticulous and requires precision engineering and expert craftsmanship. It all begins with thorough research and analysis to understand the specific requirements of each vehicle model. Wire harness manufacturers work closely with automotive engineers to design custom solutions that meet these requirements while adhering to industry standards.
Once the design phase is complete, manufacturers source high-quality materials such as copper or aluminum wires, connectors, terminals, and protective sleeves. These components are carefully selected based on requirements like current-carrying capacity, voltage rating, and environmental resistance.
The actual assembly of the wiring harness involves intricate routing of wires through the vehicle’s body, engine compartment, and interior. Manufacturers use specialized tools and equipment to ensure precise placement and secure connections. Each wire is labeled and color-coded for easy identification during installation.
Quality control is a critical aspect of the manufacturing process. Wiring harness manufacturers conduct rigorous testing to verify each harness’s integrity and functionality, including electrical conductivity tests, insulation resistance tests, and vibration tests to simulate real-world conditions.
The Role of Harness Manufacturers in Vehicle Safety
Wire harnesses play a crucial role in ensuring the safety of modern vehicles. They are responsible for transmitting signals that control essential functions such as braking, steering, and airbag deployment. Faulty wires can lead to malfunctions or failures in these critical systems, posing a significant risk to driver and passenger safety.
Manufacturers understand the importance of reliability and safety in their products. They adhere to stringent quality standards such as ISO/TS 16949 certification to ensure their harnesses meet or exceed industry requirements. Additionally, they continuously invest in research and development to incorporate advanced safety features into their designs.
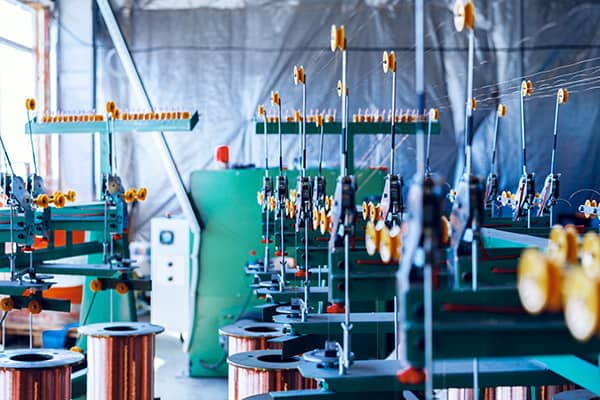
Challenges Faced by Wire Manufacturers in the Automotive Industry
The automotive industry constantly evolves, presenting unique challenges for wiring harness manufacturers. One such challenge is keeping up with rapidly advancing technologies. As vehicles become more electrified and autonomous, wiring harnesses must accommodate complex systems like advanced driver-assistance systems (ADAS) and electric powertrains.
Another challenge is cost optimization without compromising quality or performance. Automakers are under pressure to reduce production costs while meeting stringent regulatory standards. Wiring harness manufacturers must find innovative ways to streamline production processes, source cost-effective materials, and optimize designs to achieve these goals.
Furthermore, sustainability has become a key focus in the automotive industry. Wiring harness manufacturers actively explore eco-friendly materials and manufacturing techniques to minimize environmental impact. The manufacturing process includes using recyclable materials, reducing waste generation, and implementing energy-efficient production processes.
Sustainability in Automotive Manufacturing: The Impact on Harness Production
The push for sustainability in automotive manufacturing has significantly impacted wiring harness production. Manufacturers are increasingly adopting eco-friendly practices throughout the entire lifecycle of a harness, from design to disposal.
One area of focus is the use of environmentally friendly materials. Wiring harness manufacturers are exploring alternatives to traditional PVC insulation, known to harm the environment. They are investing in research and development to find bio-based or recyclable materials that offer comparable performance while reducing carbon footprint.
In addition, manufacturers are implementing energy-efficient production processes and optimizing resource utilization. They aim to minimize material waste through advanced cutting and stripping techniques and recycling scrap materials generated during production.
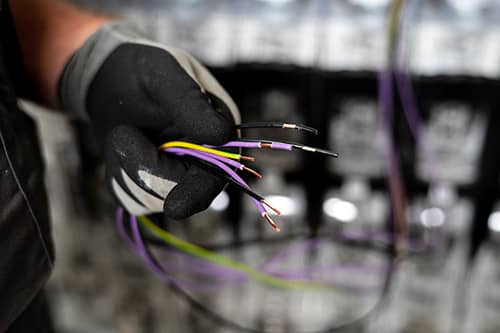
Future Trends and Forecasts
The future of wiring harnesses looks promising as technology advances at an unprecedented pace. Several trends are shaping the evolution of these critical components in automotive manufacturing.
One such trend is the increasing integration of vehicle electronics and connectivity features. As cars become more connected, wiring harnesses must accommodate a higher volume of data transmission between various systems. These integrations require advanced designs to handle increased bandwidth while maintaining signal integrity.
Another trend is the rise of electric and hybrid vehicles (EVs). These vehicles require specialized wiring harnesses capable of safely handling high-voltage power distribution systems. Wiring harness manufacturers are investing in research and development to create innovative solutions that meet the unique requirements of EVs.
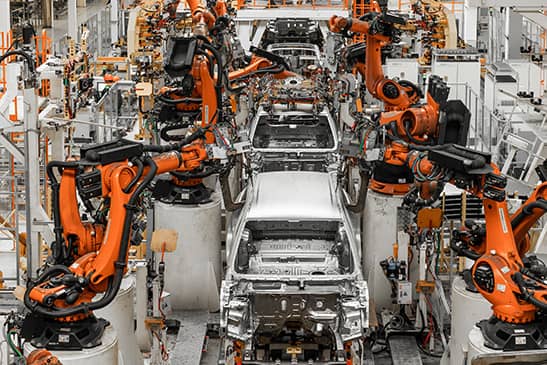
Furthermore, the advent of autonomous vehicles drives the need for advanced wiring harnesses. These vehicles rely on complex sensor systems and data communication networks to operate safely. Wiring harness manufacturers are developing intelligent harnesses to handle increased data flow and ensure reliable connectivity between various autonomous driving components.
Ensuring Quality Control: Standards and Certifications in Harness Manufacturing
Quality control is paramount in wiring harness manufacturing to ensure the reliability and performance of these critical components. Manufacturers adhere to various industry standards and certifications to demonstrate their commitment to quality.
One such standard is ISO/TS 16949, which sets quality management system requirements for automotive suppliers. This standard encompasses specific requirements for wiring harness manufacturing, including design and development, production, installation, and servicing.
In addition to ISO/TS 16949, manufacturers may comply with standards such as ISO 9001 for general quality management systems and IPC/WHMA-A-620 for wire harness assembly requirements. These standards guide processes, materials, testing methods, and product quality.
By adhering to these standards and certifications, wire harness manufacturers demonstrate their commitment to delivering high-quality products that meet or exceed customer expectations.
Wire harnesses will remain an essential component, powering the vehicles of tomorrow. With a commitment to innovation, quality, and sustainability, harness manufacturers poised themselves to meet the challenges and opportunities of an ever-changing industry, driving progress and shaping the future of automotive manufacturing.